HOW IMPORTANT IS WAREHOUSE AUTOMATION FOR OMNI-CHANNEL FULFILLMENT?
The article talks about Omnichannel fulfillment-related challenges? & How can these be solved by automation!...
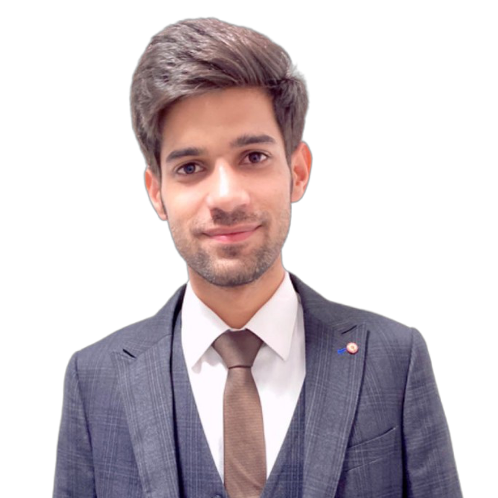
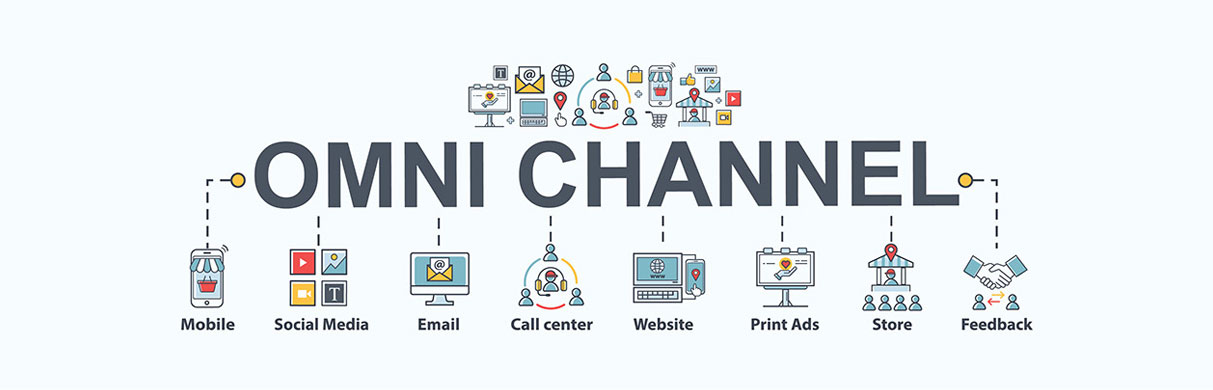
Omni-channel selling is critical for retail businesses all around the world and is the only way for small and large-scale organizations to be competitive in the long run, the rise of E-commerce and epidemics are just serving as reinforcers. Other crucial contributing factors include labor shortages, quick order delivery, rising consumer expectations, limited storage space, excessive returns, etc., etc. Brands need to organize their logistical processes around their final consumers in the future, and that is omnichannel. This article will talk about omnichannel fulfillment and how to implement the best warehouse automation plan for your organization.
What is Omni channel fulfillment? Why is it so important?
Omni-channel fulfillment is a unified strategy known to help businesses handle inventory and fulfillment of orders across multiple channels quickly and efficiently. Shoppers may now navigate between social networking platforms, e-commerce websites, and online stores. Over the last few decades, the demand for online retail has progressively expanded, requiring businesses to invest more significantly in e-commerce than in brick-and-mortar retail. With the rising trend of online shopping in the USA, retail e-commerce sales are expected to cross $1,111 billion in 2023, per Extensiv's report.
Omnichannel fulfillment strengthens the supply chain network. In-store fulfillment channels failed, as we witnessed with the outbreak of the pandemic. However, having multiple fulfillment channels allows for a rapid pivot to a new strategy, which can help mitigate disruption’s consequences. Only flexible, robust logistics networks enable omnichannel fulfillment. Quicktron’s warehouse automation has provided 3PLs and related businesses with a considerable competitive edge, reduced last-mile delivery times and costs, increased profit margins, and mitigated interruptions.
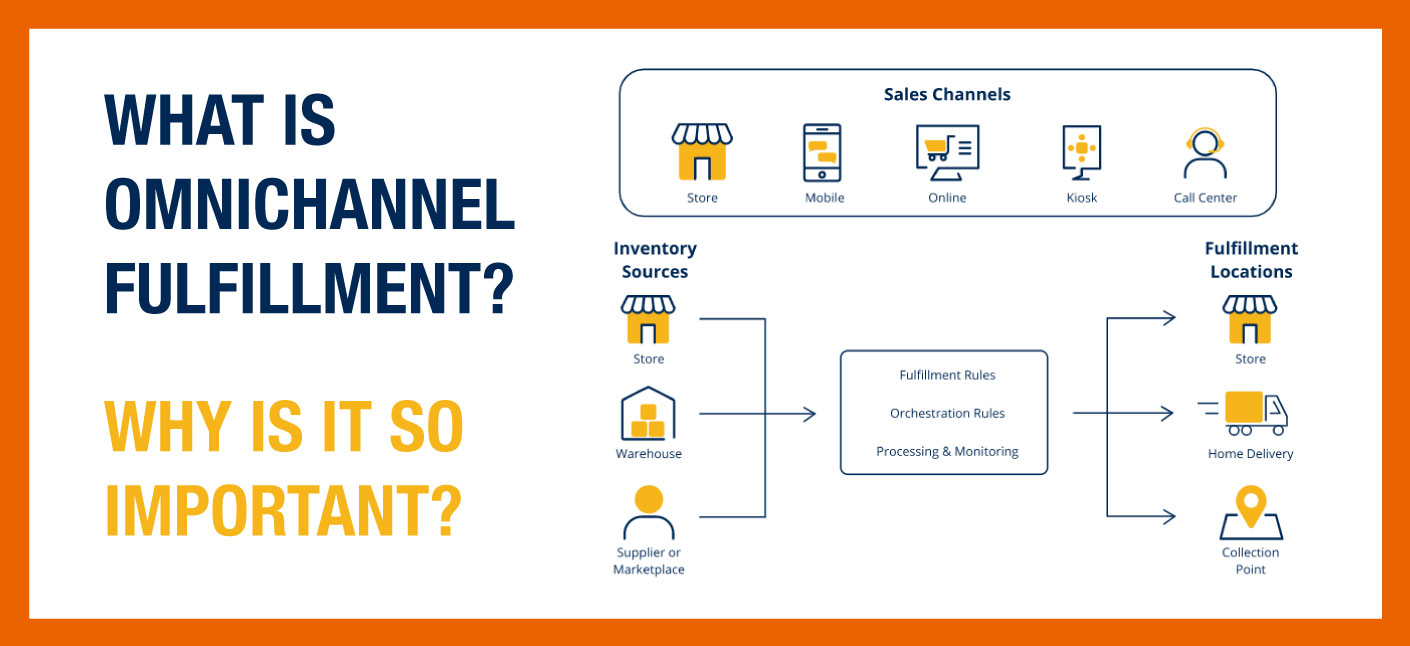
Omnichannel fulfillment challenges and solution
Omni- channel fulfillment challenges can be solved by combining inventories for both offline and online channels. Implementing core fulfillment operations and maintaining your inventory may be done more quickly, more affordably, and with less difficulty when this strategy is combined with efficient warehouse automation. Quicktron’s robotic solutions are able to adjust more swiftly to sudden (and rapid) fluctuations in demand, maintaining profitable levels of output which is why companies are investing in the optimization of intralogistics operations. Let’s discuss these briefly in the below description.
Labor shortages:
The labor shortage is the most noted phenomenon in recent years especially when we talk about logistics, the reports are really concerning. We know that humans add the most value when it comes to comprehensive and attentive process handling rather than moving things on the warehouse floor. But warehouse robots can handle the majority of the movement, setting humans free from tedious tasks, and allowing them to focus on other productive activities. This is particularly important during peak season.
Effective Space utilization:
As was already explained above, robots do the majority of the movements in warehouses. AMRs can replace people in large-scale product line relocations that no longer need to be near the dispatch area. Whether it's QuickBin or shelf based Smart picking, Quicktron's goods-to-person solutions are highly efficient in terms of space utilization. AMRs transport things to people and hallways may be made smaller because employees no longer need to go between shelves.
Cost management:
Robotic solutions not only increase worker productivity by eliminating non-value-added activities, but they are also extremely cost-effective. Quicktron robotic solutions are flexible and scalable which means the number of robots can be increased with the company’s growth. It can also be adjusted during peak days on a permanent or as-needed basis.
Returns Management:
Quicktron AMRs transport returned goods to re-shelve or scrap based on the inspection results. In the replenishment and put-away operations, they can also return examined items to the shelves. Moving or Picking robots can be utilized to pick and place returned items either onto the conveyor belt or the storage area. Furthermore, less space required for storage implies more space in the warehouse for more effective return processing.
Workplace safety:
Workplace safety is a ubiquitous concern for the manufacturing industry. How can we optimize safety?
Humans are error-prone to repetitive tasks, which account for over 33% of worker injuries during manual material handling. Whereas robots can perform these repetitive tasks more efficiently. Quicktron's AMR-powered solutions are playing a crucial role in protecting employees in warehousing facilities. Our robotic solutions are designed to move goods and dock with other equipment in the warehouses efficiently, with or without human involvement, and accelerate work in a variety of industries. ROI can be boosted by aligning worker tasks with robot capabilities since it reduces risk to employees which also lowers the cost of related compensation, medical care, and legal services.
What kind of robotic solutions Quicktron has to offer?

QuickBin is a modular Automated Storage and Retrieval System (ASRS). It's Quicktron’s patented Bin/Goods-to-person technology that optimizes warehouse operations by utilizing two types of robots and ensures unmanned/autonomous material handling. The combination of sturdy and efficient picking robots (Bin Pickers) with compact and agile moving robots (Bin Movers) enhances picking and bulk SKU handling efficiency.
Shelf-based Smart picking is also a G2P solution, which is used to transport goods to/from the workstations by moving shelves, pallets, and racks. It is effective in solving complex order portfolios, the low overlap of multi-item orders, process variability in a flexible and precise sequencing production line, high SKU count, and short order fulfillment cycle.
Conclusion
To tackle retail, e-commerce, and omnichannel fulfillment concerns, humans and robotics can operate efficiently together. It is undeniable that the world and consumers’ spending habits are changing at an alarming rate. So, only the most adaptive and agile supply chain procedures powered by warehouse automation will be able to meet the rising demands of omnichannel fulfillment. Quicktron's solutions optimize fulfillment operations through advanced navigation and control to boost productivity and accuracy. To understand how can we help you with your intralogistics operations click here.
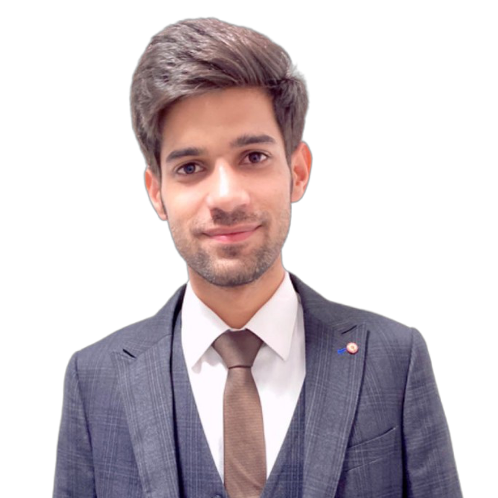
Arslan crafts compelling content, executes social media campaigns, and masters online ads, webinars, podcasts, and copywriting. He builds strong relationships with clients, empowering them with support and resources to achieve their sales goals. Leveraging data insights, he refines strategies and collaborates seamlessly to stay ahead of the digital curve.